Interlining, also known as adhesive interlining, is mainly used for clothing collars, cuffs, pockets, skirts waists, hem, and suit chests, and other parts, generally containing hot melt adhesive coating. According to the difference of the base fabric, the bonded interlining is mainly divided into two types: woven interlining and non-woven interlining.
1. Non-woven interlining, as the name suggests, is a cloth formed without weaving.
Process principle: The chemical fiber viscose is subjected to high temperature and high pressure to form a base cloth. Then, a layer of hot melt adhesive is placed on the surface of the base fabric through a coating machine and then dried to form the non-woven interlining we use.
How to use: Put the glued side of the interlining cloth on the fabric, and then heat it with a bonding machine or an iron to melt the glue on the interlining cloth, so as to achieve the effect of bonding to the fabric.
Features: cheap, soft to the touch, but not very washable (there will be requirements for the temperature of the water, normally only below 70 degrees)
2. There are woven interlinings. The commonly used equipment is a key bar loom and a water jet loom, and polyester is made into a base fabric through weaving.
The base fabric of woven interlining is divided into woven or knitted. Knitted interlining is also called: knitted fabric and knitted fabric kind.
The woven interlining is now PA coating. In the past, powder glue was usually used in the market. It is characterized by a large amount of glue and a simple production process. The disadvantage is that because of the large amount of glue, it is easy to produce glue penetration. It has now been eliminated.
The two-point process without foundation paste is characterized by easy control of the amount of glue, strong adhesion, and resistance to washing and other treatments. Now used by most manufacturers. The woven interlining is characterized by strong tensile force, good elasticity, and washing resistance.
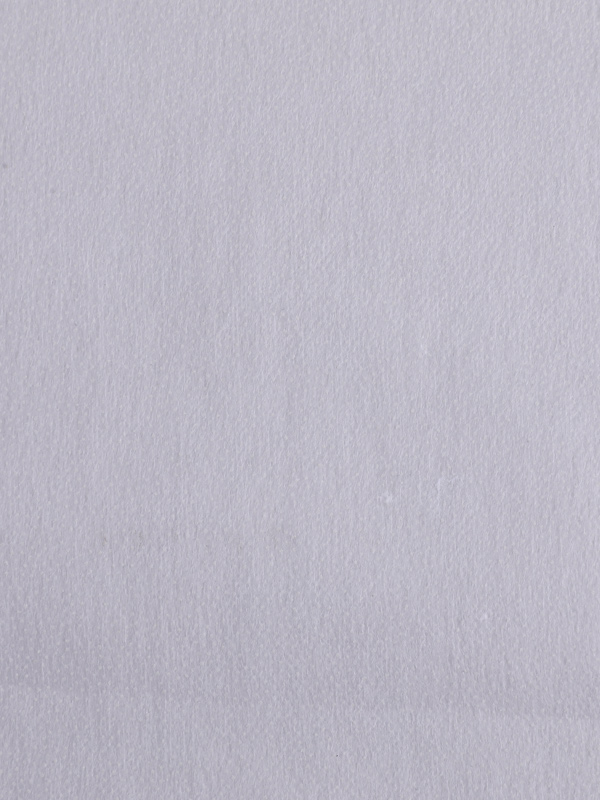