1. The same lining will have different bonding effects on different fabrics. Before choosing a bonding lining, it is necessary to distinguish whether it is a low-temperature glue or a high-temperature paddle lining, and also need to distinguish whether it is a woven lining or a non-woven lining.
Under the same bonding conditions, due to the influence of the fiber composition of the fabric, the twist of the yarn, the tightness of the organizational structure, etc. on the bonding strength, the following is a comparison of the peel strength of some different fabrics after bonding.
2. The effects of different fabric materials on the temperature of the bonding surface are: there are several stacking methods and characteristics of spun interlining and fabrics. Standard stacking method: that is, the fabric is on the bottom and the back is facing up, the interlining is on the top and the bonding surface is facing down. The effect of standard overlapping bonding is better, but the effect is low, and the fabric is easy to stick and stain.
The coat requires proper elasticity, and the shirt collar needs to choose a resin collar lining with a certain degree of stiffness. The increase in stiffness results in a corresponding increase in stiffness.
3. Bonding time The bonding effect between the interlining and the fabric is greatly affected by time, because the flow of hot melt adhesive into the fabric is related to the peel strength and bonding time of a certain time process. The bonding of the two layers of fabrics depends on the short time of hot melt adhesive connecting the two layers. The hot melt adhesive lacks melting and cannot well infiltrate the fabric, so the peel strength is low, but the pressing time is too long. A large amount of melt glue will infiltrate into the fabric, and the length of pressing time should be selected according to the density and thickness of the fabric.
4. Bonding pressure The pressure and pressure time during bonding and the pressure during bonding are mainly to eliminate the gap between the two layers of fabrics so that the hot melt adhesive is squeezed into the fabric by an external force. The pressing form of the hot melt adhesive is plane pressing, which makes the hot melt adhesive pressurized from the glass state (solid-state) until it reaches the viscous flow state. Heating and pressing are synchronized in time because the pressing time is longer, so the adhesion fastness is higher than that of the belt pressing machine, but it is easy to penetrate;
5. The pressurization form of the rolling ironing machine is linear pressurization. This pressurization method is to heat the fabric and the hot melt adhesive at the same time and pass through the oven at the same time. Because the two layers of unbonded fabrics are not tightly attached in the heating at this time, the interlining hot melt adhesive cannot be well bonded to the fabric, so the roller belt pressing machine (except those with pre-pressing and preheating) is not as strong as the plate pressing and bonding, and the effect is more obvious on difficult-to-stick fabrics.
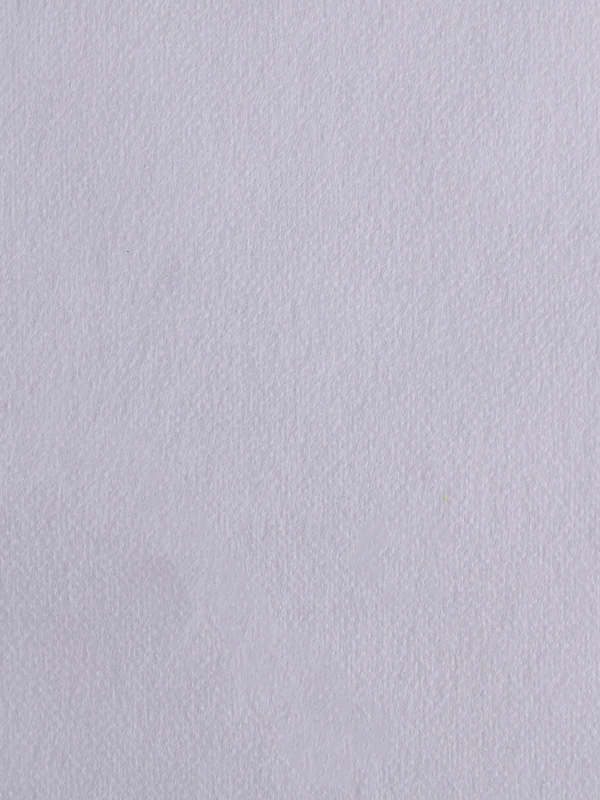